Key Mechanisms Behind Battery Degradation and How to Address Them
Batteries are widely used across various applications, from everyday electronics to electric vehicles and large-scale energy storage systems. However, with increased use over time, battery aging is inevitable. This leads to performance degradation and shortened cycle life, which not only affects device reliability but also poses challenges to sustainable development in related industries. A deep understanding of battery aging mechanisms is crucial for improving battery longevity, enhancing performance, and driving technological advancements.
For those looking to extend battery lifespan, the Battery guide on lithium battery aging provides useful strategies and background.
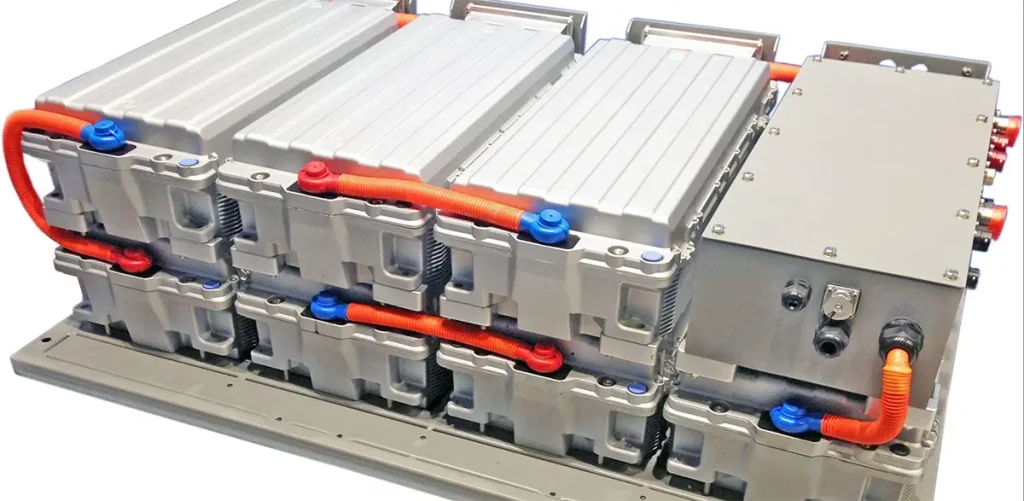
Electrode Material Degradation
Lattice Stress from Lithium-Ion Intercalation/Deintercalation
During charge and discharge cycles, lithium ions repeatedly intercalate and deintercalate between the positive and negative electrode materials. For example, in graphite anodes commonly used in lithium-ion batteries, lithium ions embed between graphite layers during charging, expanding the layer spacing. During discharge, they exit and the spacing contracts. This repeated expansion and contraction acts like a compressed and stretched spring, imposing mechanical stress on the graphite lattice. Over time, this stress causes lattice distortion, misalignment, or collapse, impairing lithium-ion transport pathways, increasing internal resistance, reducing efficiency, and causing capacity fade.
Phase Transition and Loss of Activity in Cathode Materials
Cathode materials like lithium cobalt oxide (LiCoO₂) and nickel cobalt manganese oxide (NCM) undergo complex phase transitions during prolonged cycling. In the case of LiCoO₂, as lithium is extracted during charging, the crystal structure shifts from hexagonal (alpha-NaFeO₂ type) to a monoclinic form. These phase changes are often irreversible, creating inactive structures that reduce the number of electrochemically active sites. Additionally, phase changes lower the material’s electronic conductivity and lithium-ion diffusion coefficient, further accelerating battery aging.
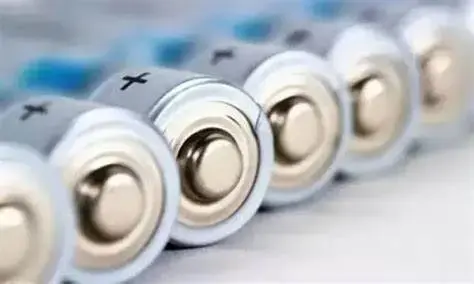
Structural Failure in Anode Materials
Some anode materials experience significant volume expansion during lithium-ion intercalation. Silicon-based anodes, for example, can expand by 300–400%, despite their high theoretical capacity. This expansion leads to repeated swelling and contraction of silicon particles during cycling, resulting in poor particle contact, cracking, and increased internal resistance. Cracks also expose fresh material to the electrolyte, initiating more side reactions and accelerating degradation. Over time, these cracks grow, causing particle pulverization and loss of active material, severely reducing capacity and cycle life.
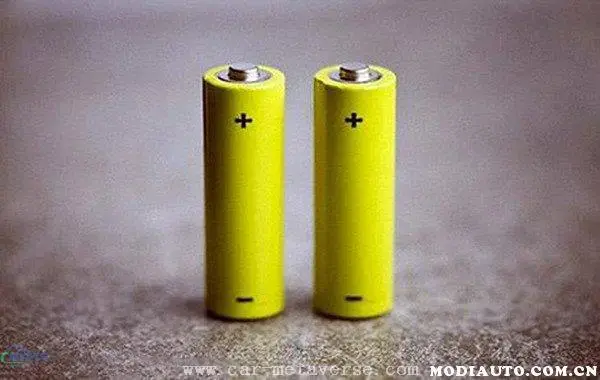
Electrolyte Decomposition and Consumption
Oxidation of Organic Solvents at High Temperature
Organic solvents in electrolytes (e.g., ethylene carbonate [EC], dimethyl carbonate [DMC]) serve as lithium-ion carriers. At high temperatures, these solvents become unstable and oxidize on the high-voltage cathode surface. For instance, EC may undergo ring-opening oxidation, generating gases like CO₂ and CO and various organic byproducts. These gases increase internal pressure and may cause battery swelling or rupture. Meanwhile, the byproducts form a passivation film that, while protective to some extent, increases internal resistance and energy loss, reducing efficiency.
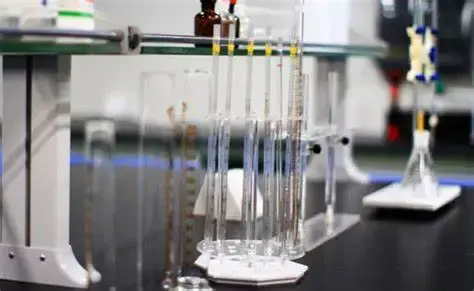
Irreversible Reactions and Lithium Salt Consumption
Lithium salts (e.g., LiPF₆) are key to lithium-ion transport but can react irreversibly with impurities, defects, or other electrolyte components. Moisture on cathode surfaces can react with LiPF₆ to produce hydrofluoric acid (HF), a corrosive agent that damages electrodes and consumes lithium ions. Transition metals (e.g., Co, Ni) may also dissolve into the electrolyte and displace lithium ions, reducing lithium salt concentration. This weakens ion transport and overall performance, accelerating battery aging.
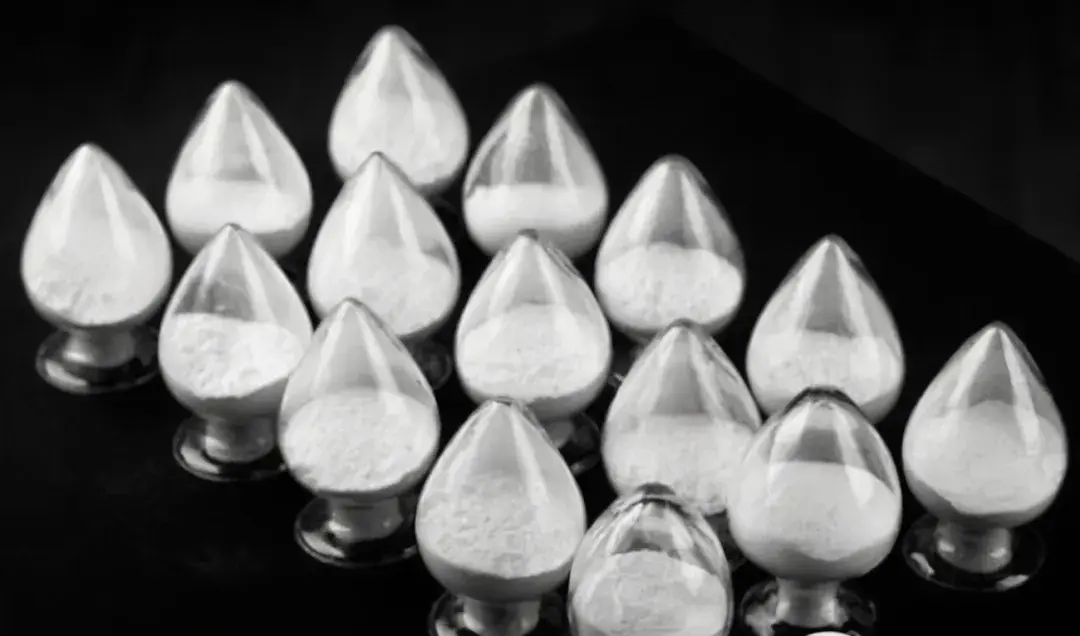
Dendrite Growth and Associated Risks
Formation Conditions and Process
Lithium dendrites form when lithium ions deposit unevenly and too rapidly on the anode surface, often due to high charging current. Localized lithium concentration spikes lead to preferential deposition, resulting in needle-like dendritic structures. Factors influencing dendrite formation include current density, anode surface properties, electrolyte composition, and temperature. Surface roughness and defects, as well as electrolyte additives, all play roles in lithium deposition behavior.
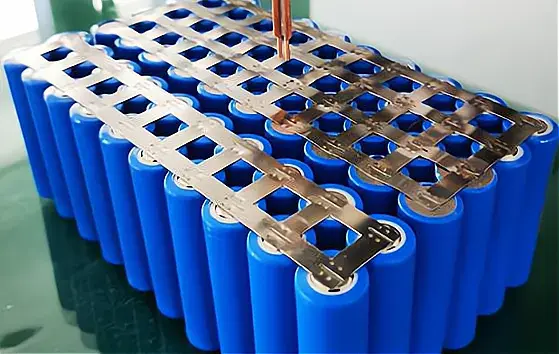
Safety and Performance Hazards
Lithium dendrites pose serious risks. If long enough, they can pierce the separator, causing internal short circuits and triggering large current discharge. This generates heat, possibly leading to thermal runaway, fire, or explosion. Dendrites also consume active lithium, reducing capacity and increasing internal resistance, ultimately degrading efficiency and cycle life.
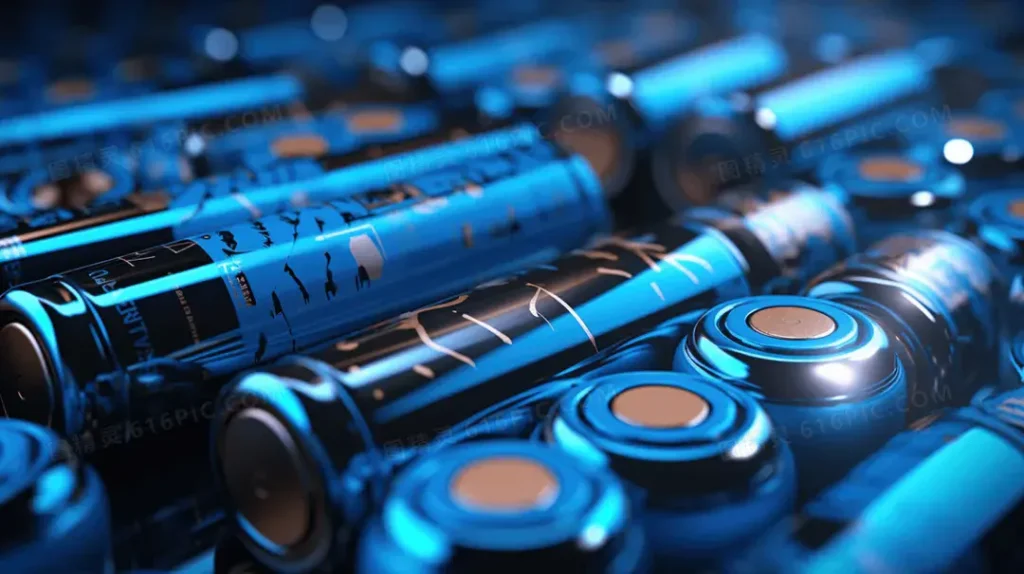
Internal Corrosion and Contamination
Impurities and Side Reactions
Impurities from raw materials, manufacturing, or long-term use can cause adverse reactions. Metals like iron or copper can dissolve and redeposit during cycling, altering anode surface conductivity and lithium deposition patterns, leading to localized shorts and capacity loss. Moisture can hydrolyze lithium salts, producing HF and corroding electrode materials, disrupting chemical balance, and accelerating battery aging.
Metal Component Corrosion
Battery components such as current collectors and tabs can corrode over time. Aluminum, used in current collectors, is susceptible to acid or base-induced corrosion. In acidic environments, aluminum reacts with H⁺ ions and dissolves; in alkaline electrolytes, it forms corrosive byproducts that block electrode pores and disrupt internal structure, harming performance and reducing cycle life.

Battery aging is a complex process driven by multiple intertwined factors: electrode structural changes, electrolyte degradation, dendrite growth, and internal corrosion. Research from institutions like the National Renewable Energy Laboratory (NREL) provides further insight into how internal resistance and aging dynamics evolve in lithium-ion systems. Studying these mechanisms supports the development of advanced materials, optimized battery designs, and smart management strategies to improve reliability, extend life, and advance battery technology toward higher performance, safety, and sustainability.